3D-Druck in der Lebensmittelindustrie
Schicht für Schicht zum fertigen Bauteil
Der 3D-Druck gehört neben Robotik, Digitalisierung und Machine Learning zu den großen Zukunftsthemen. Bei dem Verfahren, auch additive Fertigung genannt, wird ein mittels CAD erstelltes 3D-Modell in zweidimensionale Schichten umgewandelt, die dann beim Drucken nacheinander aufgetragen werden. Die Vorteile des Verfahrens liegen in der schnellen Realisierung von innovativen Ideen, der Designfreiheit und der weitgehenden Geometrieunabhängigkeit – und dies bei geringerem Ressourceneinsatz, da während der Herstellung kaum Abfälle entstehen.
Speziell bei bionischen Leichtbaustrukturen, die sich mit traditionellen Fertigungsmethoden wie CNC-Fräsen oder -Drehen nur schwer realisieren lassen, spielt die disruptive Technologie ihre Vorzüge aus. Als besonders geeignet erweisen sich beispielsweise Waben- oder Gitterstrukturen. Sie überzeugen nicht nur durch hohe Stabilität, sie sind auch deutlich leichter im Gewicht als massive Bauteile – beides Aspekte, mit denen sich Reinhard Ortner beschäftigt, Produktionstechnologe bei Krones in Neutraubling. Exemplarisch dafür steht ein 3D-gedruckter Dosenwender, der in den Abfüllmaschinen von Krones zum Einsatz kommt. Seine Funktion: Getränkedosen, die ihn durchlaufen, um 180 Grad zu drehen. Früher aufwendig in Edelstahl gefertigt, setzt Krones jetzt auf den Jet Fusion 5200 3D-Drucker von HP.
Ortner, der den Unternehmensbereich Additive Fertigung leitet, ist überzeugt: Die generative Komponentenfertigung bietet für den Maschinenbau viele Chancen. Mit dem 3D-Druck lassen sich kleinste Stückzahlen kosteneffizient realisieren, etwa beim Anfertigen von Prototypen. Für die Ersatzteilversorgung älterer Maschinen ist die Technologie ebenfalls interessant, denn die Komponenten müssen nicht mehr vorrätig gehalten werden. Stattdessen können sie nach Konstruktionsanpassungen kurzfristig ohne eigens dafür angefertigtes Werkzeug reproduziert werden. Lebensmittelhersteller profitieren so nicht nur von einer schnellen Verfügbarkeit, sondern auch von individuell auf ihre Maschine zugeschnittenen Bauteilen – ganz ohne komplexe Lieferketten.
Der Dosenwender aus dem Drucker
Eine Herausforderung ist die Qualitätssicherung. Sowohl für die additiven Herstellungsverfahren als auch für die produzierten Bauteile liegen oft keine ausreichenden Messmethoden und Standards vor. Für die Umsetzung des 3D-gedruckten Dosenwenders galt es deshalb diverse Faktoren zu berücksichtigen, denn die Abfülllinien von Krones verarbeiten bis zu 130.000 Dosen innerhalb einer Stunde. „Jedes verbaute Teil muss den hohen Anforderungen der Anlagen-Performance entsprechen. Darunter fallen neben der Stabilität auch die Elastizität und Resistenz des Materials gegen Reinigungsmittel“, erläutert Ortner. Das Entwicklungsteam musste eine Vielzahl an Punkten analysieren, wie die Kinematik, also den optimalen Bewegungsablauf der Getränkedosen beim Wenden. „Hinzu kamen tribologische Eigenschaften, sprich das Reibungsverhalten zwischen den Dosen und dem Material“, ergänzt Andreas Neuber, Entwicklungsingenieur mit Schwerpunkt Additive Fertigung bei Krones.
Bei den Berechnungen haben sich dann aber die Vorteile des additiv gefertigten Dosenwenders gezeigt: Der Einsatz des 3D-Druckers ermöglichte eine Gewichtsreduktion des Bauteils um rund 80 Prozent. Ein weiterer Pluspunkt: Die ideale Dosenführung lässt sich beliebig oft reproduzieren und unkompliziert an neue Behälterformate anpassen, denn das geringere Gewicht bedeutet ein einfacheres Handling beim Umrüsten der Abfüllanlagen, also etwa beim Wechsel von einer 0,5 Liter Dose auf eine 0,3 Liter Dose. Dieser gelingt der jetzt ohne Werkzeug.
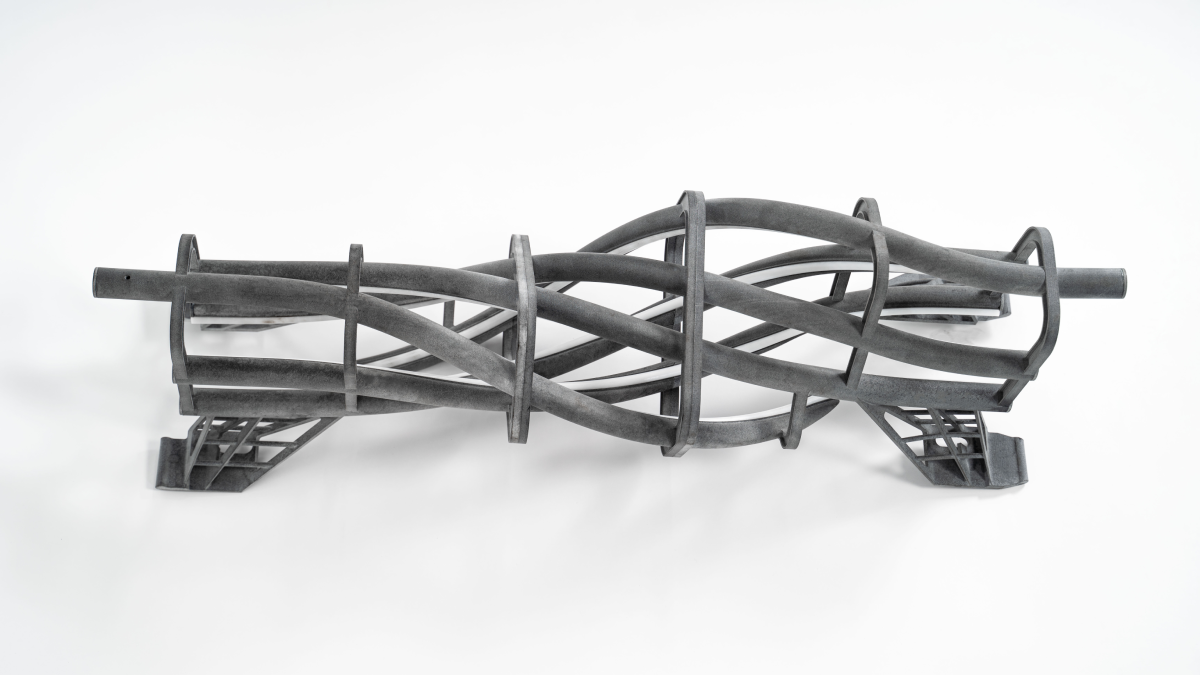
Der mittels 3D-Druck hergestellte Dosenwender von Krones kann in einer Stunde bis zu 130.000 Dosen für die Abfüllung um 180 Grad drehen. Copyright: © Krones
Aufgedruckte Sensoren für mehr Präzision
Die Multi Material Jetting (MMJ)-Technologie ist für viele Experten die nächste Stufe in der additiven Fertigung. Mit bis zu sechs Druckköpfen, und damit bis zu sechs unterschiedlichen Materialien, erreicht die jüngste Generation von Hightech-Druckern Bauteilgenauigkeiten von 70 bis 100 Mikrometer. Mit einem zusätzlichen Lasermodul, das während des 3D-Drucks Material abträgt, poliert oder die Oberflächen strukturiert, werden Rauigkeiten von unter einem Mikrometer erreicht. Damit entfällt die aufwendige Nachbearbeitung der Bauteile. Hersteller können so ihre Fertigung hinsichtlich Zeit und Kosten weiter optimieren. Dazu tragen auch KI-Methoden zur Qualitätssicherung bei, wie eine Defekterkennung und eine automatische Anpassung der Prozessparameter während des Drucks. So lassen sich funktionalisierte Bauteile oder ganze Baugruppen, etwa mit integrierter Sensorik oder Aktorik, innerhalb eines Prozesses drucken.
Durch die neue Materialvielfalt sind der Kreativität kaum noch Grenzen gesetzt. Es lassen sich Materialien mit definierten Eigenschaften herstellen und kombinieren, wie elektrisch leitfähig und elektrisch isolierend, dicht und porös, hart und duktil oder auch magnetisch und nicht magnetisch. Eine beispielhafte Innovation, an der das Fraunhofer-Institut für Lasertechnik ILT arbeitet, ist die nahtlose Einbindung von Sensoren während des additiven Herstellungsprozesses. Mithilfe von 3D-Strukturdruckverfahren wie der Laser Powder Bed Fusion (LPBF) lassen sich gedruckte Sensoren direkt in die Bauteile integrieren, während sie entstehen. Dies ermöglicht nicht nur die präzise Platzierung von Sensoren für anspruchsvolle Zustandsanalysen (Condition Monitoring), sondern auch den Schutz dieser Sensoren vor mechanischen Umwelteinflüssen. „Die Geometrie der Sensoren kann je nach Bauteil individuell angepasst werden. Zukünftig sind sogar weitere Funktionselemente wie integrierte Heizer denkbar“, sagt Samuel Fink, Gruppenleiter Dünnschichtverfahren am Fraunhofer ILT.
Werkzeuge auf Pay-per-Use-Basis
Bei all der Begeisterung über die künftigen technischen Möglichkeiten, fordern Lebensmittelproduzenten vor allem aber eines: Fehlerfrei funktionierende Lösungen, um schon heute neue Ideen rasch und kostengünstig in konkrete Produkte umzusetzen. Die Schubert Group zeigte auf der Anuga FoodTec 2024, was erforderlich ist, damit aus einem 3D-gedruckten Objekt ein einsatzbereites Werkzeug für eine Verpackungsmaschine wird. Das Crailsheimer Unternehmen baut mittlerweile keine Verpackungsmaschine mehr ohne selbst gedruckte Formatteile. So nutzt die Molkerei Heinrichsthaler für das Verpacken ihrer Grillkäsetaler einen Schubert-Kartonierer, dessen Roboter mit entsprechenden Vakuumsaugern ausgerüstet sind. Zum Einsatz kommt dabei eine Schubert-Eigenentwicklung: die PARTBOX, ein industrietauglicher 3D-Drucker.
Bauteile für den Verpackungsprozess selbst zu drucken, bringt viele Vorteile: optimal angepasste Roboterwerkzeuge für alle denkbaren Produkte, kein langwieriger Transport neuer Formatteile, schneller Ersatz bei defekten Werkzeugen und die Möglichkeit, Formatsätze für geänderte Produkte selbst herzustellen. „Wir sind der Überzeugung, dass Bauteile zu der Zeit und an dem Ort produziert werden sollten, wann und wo sie gebraucht werden“, erklärt Conrad Zanzinger, Technischer Leiter bei Schubert Additive Solutions. Gegründet wurde das Unternehmen von der Schubert Group, um Kunden die Möglichkeit zu geben, die digitalen Fertigungsdaten der bestellten Teile zu erhalten und diese mittels additiver Fertigung auf Pay-per-Use-Basis zu produzieren.
Wichtig war es Schubert Additive Solutions mit dem PARTBOX-Drucker, eine Lösung zu gestalten, die ohne großes Know-how genutzt werden kann. So können nicht nur Teile für Schubert-Verpackungsmaschinen hergestellt werden, sondern auch jene von anderen Maschinenbauern. Besitzt der Kunde eine Maschine von Schubert, kann er die Druckjobs für die dazugehörigen Teile auf der Streaming-Plattform PARTBOX abrufen. Sollen neue Produkte auf der Maschine verarbeitet werden, entwickelt Schubert passende Formatteile und lädt dann den Druckjob hoch. „So kann der Kunde ganz einfach in seinem Unternehmen mit unserem selbstentwickelten Drucker das benötigte Teil drucken“, sagt Zanzinger.
3D-Druck in hygienekritischen Branchen
Alle Teile, die für den Kontakt mit Lebensmitteln bestimmt sind, müssen entsprechend zertifiziert sein. Schubert Additive Solutions liefert mit dem Kunststoff "PARTBOX Black" auch das passende Druckmaterial. Der Unterschied zu marktüblichen Filamenten liegt in einem für das FDM-Druckverfahren (Fused Deposition Modeling) optimierten Polyamid. Das Material ist lebensmittelkonform und mit einem Metalldetektor detektierbar. Darüber hinaus weist es gute mechanische Eigenschaften und eine hohe Temperaturbeständigkeit auf. Dadurch können im Druckprozess sehr glatte Oberflächen erzielt werden.
Die Beispiele zeigen: Der 3D-Druck ermöglicht eine individuelle, werkzeuglose Fertigung von komplexen Geometrien. Eine Technik der Zukunft, die jedoch Herausforderungen für den Einsatz in hygienekritischen Bereichen wie der Lebensmittelindustrie mit sich bringt. Beim metallischen 3D-Druck, wie dem Laser-Strahlschmelzen, weisen die entstehenden Oberflächen aufgrund ihrer hohen Rauheit oft nicht die nötigen hygienegerechten Oberflächeneigenschaften auf. Die Entwicklung und Validierung spezieller Finishing-Strategien, um produktberührte Oberflächen zu perfektionieren, ist eine weitere Hürde, die es in der additiven Fertigung für die Lebensmittelindustrie in den kommenden Jahren zu überwinden gilt.
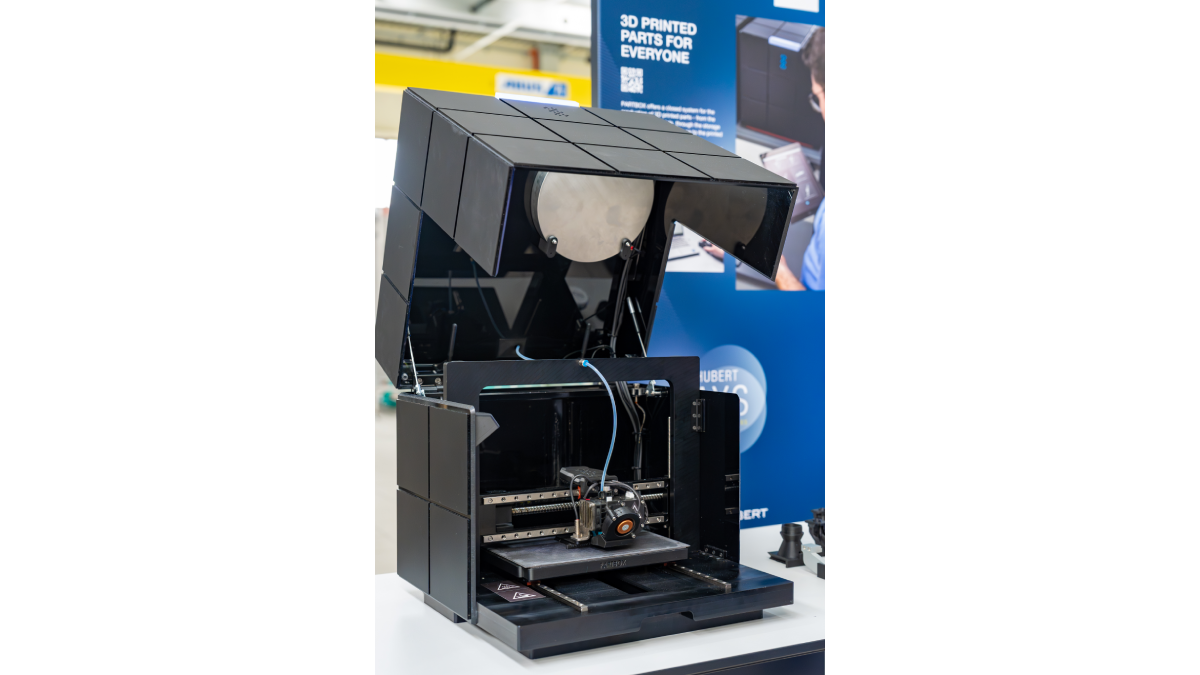
3D-Teile per Klick produzieren: Über die PARTBOX Streaming-Plattform von Schubert Additive Solutions lassen sich Druckjobs direkt auf dem 3D-Drucker starten. Copyright: ©Press4Process