Die Zukunft der Ventiltechnologie
Software lokalisiert fehlerhafte Füllventile
Prozessventile braucht es in der Lebensmittel- und Getränkeindustrie für zahlreiche Anwendungen. Trotzdem ist eine kontinuierliche Wartung und Kontrolle der Armaturen und ihrer Dichtelemente häufig noch auf Augenschein gegründet. Was der Markt in Zeiten zunehmender Automation jedoch fordert, ist der Einsatz von Inspektionstechnik, die Probleme und Fehler aufzeigt, bevor sie zum Stillstand von Anlagen führen. Ein digitales Managementsystem bietet da eine ganze Palette an Vorteilen im Sinne des Condition Monitoring – angefangen bei der Minimierung der Stillstandzeiten bis hin zur Möglichkeit der Abschaltung einzelner Ventile ohne Produktionsunterbrechung. Das Innocheck MMS von KHS ist ein Beispiel für eine solche Anwendung beim Füllen und Verschließen von Dosen. Es lokalisiert fehlerhafte Füllventile sowie Verschlusselemente und wertet diese durch eine exakte Auslesung kompletter Parameter aus. „Anhand der Auswertung können Abfüller fehlerhafte Füllungen auf einzelne Ventile zurückführen und frühzeitig eingreifen,“ erklärt Henrik Kahrmann vom Produktsupport Etikettier- und Inspektionstechnik bei KHS.
Zustände umfassend überwachen
Condition Monitoring-Systeme neuster Generation sind in der Lage, kleinste Zustandsänderungen noch früher zu erkennen als bisher. Der Einsatz fortschrittlicher Sensorik übernimmt dabei eine Schlüsselrolle. Sie überwacht laufend Messgrößen wie Temperatur, Luftfeuchtigkeit und Luftdruck, überträgt diese über vorhandene Kommunikationsschnittstellen, sodass sie gezielt auf Anomalien oder sich abzeichnende negative Trends hin analysiert werden können. Sich verschlechternde Gerätezustand und Betriebsbedingungen lassen sich so erkennen, lange bevor es zu einer tatsächlichen Störung kommt.
Zu den elementaren Größen bei pneumatisch betätigten Prozessventilen zählt etwa der Steuerluft-Versorgungsdruck. Er ist nach wie vor eine der Hauptursachen für Fehler im Ventilbetrieb. Wird er gezielt überwacht, lässt sich sofort erkennen, ob dieser zu niedrig, zu hoch oder instabil ist. Der Ventiltechnikspezialist Gemü schlägt diesen Weg bei der neuen Produktgeneration Leap Lean ein. Ein zentraler Bestandteil ist der 12A0 – ein intelligenter, elektrischer Stellungsrückmelder mit integrierten Hall-Sensoren. Sie erfassen Parameter wie Luftfeuchtigkeit und Betriebsdruck. Zudem bietet der 12A0 modernste Kommunikationsschnittstellen wie ASi-5 sowie IO-Link. Mit der Gemü App und einer Bluetooth-Verbindung lassen sich die Sensorwerte direkt am Smartdevice anzeigen. Dies soll bei Störfällen die Fehlersuche erheblich erleichtern und bietet zudem die Möglichkeit, den aktuellen Zustand vom Ventil bei Wartungs- oder Servicearbeiten direkt abzulesen.
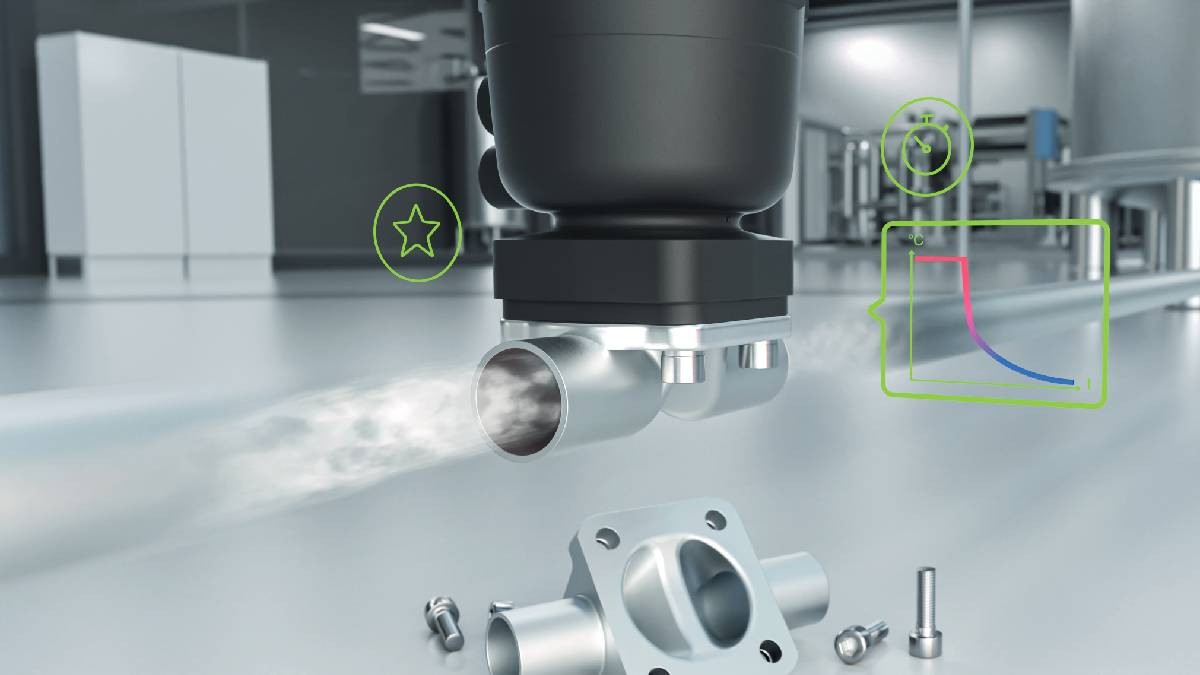
Die Rohrumformgehäuse haben eine erheblich geringere thermische Masse als Schmiede- und Gussvarianten. Ein Vorteil, der umso deutlicher wird, je größer die Nennweite ist. © Bürkert Fluid Control Systems
Anlagenverfügbarkeit im Sinne der Nachhaltigkeit
Eine schlanke Verkabelung und der Einsatz von intelligenten Steueraufsätzen für Prozessventile, die beispielsweise über IO-Link eingebunden werden, sorgen auch bei den Lösungen von Bürkert für bessere Anlagenüberwachung und reduzieren gleichzeitig den Installationsaufwand. Doch überall, wo Anlagen auf eine hohe Verfügbarkeit optimiert sind, geht es auch um Nachhaltigkeit und möglichst geringe Betriebskosten. Alle verbauten und an den Prozessen beteiligten Komponenten müssen dazu beitragen. Vor allem in SIP-Prozessen werden große Mengen an Reinstdampf benötigt, um die massereichen Ventilkörper auf Sterilisationstemperatur zu bringen. Gleichzeitig verkürzt sich die Zeit, in der produziert werden kann, da sich die Gehäuse nur langsam erhitzen und abkühlen.
Zu den Entwicklungen der Fluidikexperten aus Ingelfingen zählt ein Rohrumformgehäuse mit einer erheblich geringeren thermischen Masse. „Da es sich bei SIP-Prozessen deutlich schneller aufheizen und abkühlen lässt als konventionelle Schmiede- oder Gussgehäuse, ist weniger Reinstdampf und Energie nötigt, um die Ventilkörper auf Sterilisationstemperatur zu bringen“, erklärt Michael Wiedmann. „Bei einer Temperaturdifferenz von 100 Kelvin können sich pro SIP-Zyklus Energieeinsparungen von über 50 Prozent ergeben. Geht man etwa von einer Applikation mit 100 Ventilen aus, spart das 875 Kilogramm Kohlendioxid pro Jahr“, so der Produktmanager Membranventile bei Bürkert Fluid Control Systems.
Robustes Leichtgewicht
Die Grundlage dafür liefert das spezielle Fertigungsverfahren: Die Membranventilgehäuse werden im Rohrumformverfahren, auch bekannt unter dem Begriff Hydroforming, hergestellt. Das heißt, ein metallisches Rohr wird in einem geschlossenen Werkzeug mit Innendruck in mehreren Schritten inklusive Wärmebehandlung zum Ventilgehäuse geformt. So können beispielsweise für die Gehäuse der Ventile die gleichen Rohrmaterialien verwendet werden, die in der Anlage eingesetzt und dafür zugelassen sind. Außerdem sind Montage oder Schweißoperationen wie bei einer Halbschalenbauweise nicht mehr notwendig und die Gehäuse wiegen kaum mehr als ein Rohr gleicher Länge. Im Gegensatz zu Gussgehäusen entstehen bei der Fertigung keine Lunker oder andere Unreinheiten, die immer ein Kontaminationsrisiko oder Fertigungsausschuss bedeuten. Ein weiteres Plus für die Reinigung: Durch eine direkte Rohr-zu-Rohr-Verschweißung kann sich nichts festsetzen.
Weniger Stress für die Membranen
Gleichzeitig steigt die Produktivität der Anlage, da sich durch den schnellen Aufheiz- und Abkühlprozess die Nebenzeiten für die Reinigung verkürzen. Je öfter gereinigt werden muss, desto mehr profitiert der Anwender davon. Da die Ventile durch die vergleichsweise geringe thermische Masse sich bei den SIP-Prozessen schneller aufheizen und abkühlen, reduziert sich auch der thermische Stress für die temperaturempfindlichen Membranen. Sie halten deutlich länger als das bei anderen Gehäuseausführungen üblich ist. Je nach Anwendung kann ihre Lebensdauer dadurch mehr als verdoppelt werden, was die notwendigen Servicezyklen verlängert und ebenfalls zur Nachhaltigkeit beiträgt.
„Schlussendlich haben die Membranventile im Rohrumformgehäuse auch für die Anlagenbauer einen nicht zu unterschätzenden Nutzen“, ist Wiedmann überzeugt. Denn: „Anders als bei Schmiede- oder Gussgehäusen müssen sie in den meisten Fällen keine zusätzlichen Abstützungen für die Ventile vorsehen, was Konstruktion und Montage deutlich erleichtern kann, Arbeit spart und damit ebenfalls die Kosten senkt.“
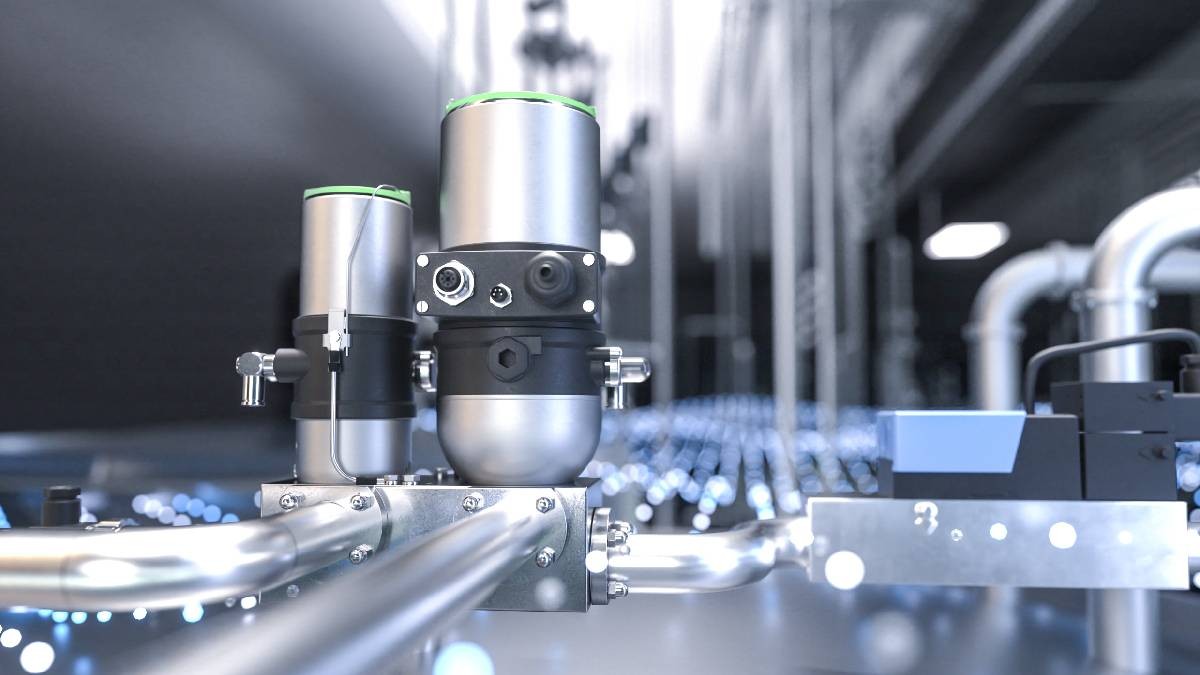
Bürkert begleitet Anwender von der Planung bis zur Inbetriebnahme ihrer Infrastruktur zur Automatisierung fluidischer Regelkreise. © Bürkert Fluid Control Systems
Datenlogging für Ventile zur Prozessregelung
Auch in der Prozessregelung kommen Ventile von Bürkert zum Einsatz, um den Strom von Flüssigkeiten oder Gasen zu regeln. Für Ventile, die zum Beispiel zur Regelung der Prozesstemperatur eingesetzt werden, bietet Bürkert ein automatisiertes Datenlogging. Dadurch lässt sich Optimierungspotenzial schneller und kostengünstig aufspüren, was Instandhaltungsaufwand reduziert sowie Anlagenstillstand verhindert und dem Servicetechniker so manche Reise erspart. Ein vorkonfiguriertes Logging-Modul wird dazu eine bestimmte Zeit auf die Serviceschnittstelle des Regelsystems gesteckt und danach an den technischen Service zur Analyse geschickt. Über eine mobile Internetverbindung ist es möglich, die Daten direkt in die Analyse-Cloud zu übertragen. Ein Mobilfunk-Router verbindet sich drahtlos mit der Cloud und wird mit einer Halterung am Regelsystem befestigt. Die Fluidik-Experten können so auch individuelle Lösungen zum automatisierten Datenlogging realisieren.
Aus Erfahrung wird ein Produkt
Anlass für die Entwicklung der neuen Servicedienstleistung war ein Szenario aus der Praxis: Ein Prozessregelsystem mit Element-Sitzventil sorgte in einer Anlage für die Temperaturregelung. Der Antrieb des Ventils verschliss in unverhältnismäßig kurzer Zeit, was sich durch eine Leckage nach außen bemerkbar machte. Dadurch musste der komplette Antrieb des Ventils ausgetauscht werden. Die Anlage stand deshalb häufiger, jeder Austausch kostete Geld und Medium ging verloren. Auf der Suche nach der Ursache loggte ein Mitarbeiter des Serviceteams die Daten vor Ort per Laptop. Die Analyse ergab: Schuld war ein ungünstig eingestellter Regler. Er regelte permanent kaum merklich nach, was zum Verschleiß der Spindeldichtung führte. Durch einen Serviceeinsatz konnten die Parameter entsprechend angepasst und somit die Lebensdauer des Regelventils spürbar verlängert werden. Diese Erfahrung war für die Fluidikexperten die Initialzündung für das automatisierte Datenlogging. Um Datensammeln und Fehlersuche zu erleichtern, brachten sie das automatisierte Datenlogging in seinen unterschiedlichen Varianten auf den Weg. Dafür ist kein Eingriff in die Steuerung notwendig und die Eigenschaften des Regelventils bleiben unberührt.