In drei Schritten zur digitalisierten Lebensmittelproduktion
Erster Schritt: Maschinendaten erfassen
Eine nachhaltige Prozessoptimierung beginnt mit der umfassenden Erfassung von Daten. Doch gerade in der Lebensmittelindustrie stoßen Unternehmen häufig auf Herausforderungen wie die Heterogenität ihrer Maschinenlandschaft oder die Integration bestehender Systeme in eine digitale Umgebung. Die Datenerfassung stellt Unternehmen vor die folgenden Herausforderungen:
- Alte Maschinen: Ältere Anlagen verfügen oft nicht über digitale Schnittstellen oder Standardprotokolle, die eine nahtlose Integration ermöglichen.
- Datenvielfalt: Unterschiedliche Maschinentypen und Prozesse generieren heterogene Daten (Formate), die schwer standardisierbar sind.
- Sensible Daten: Die zunehmende Vernetzung von Maschinen erhöht die Gefahr von Daten- und damit Know-How-Diebstahl und die Gefahr von Fremdeinwirkungen durch Hackerangriffe.
Neben der Effizienzsteigerung ist die Einhaltung gesetzlicher Anforderungen ein entscheidender Faktor. Besonders in der Lebensmittelproduktion spielt die HACCP-Konformität (Hazard Analysis and Critical Control Points) eine zentrale Rolle. Diese verlangt die kontinuierliche Überwachung und Dokumentation kritischer Kontrollpunkte, etwa Temperatur oder Druck, um die Produktsicherheit zu gewährleisten.
Hier kommen Manufacturing Execution Systems (MES) ins Spiel. Diese Systeme ermöglichen es, Daten direkt an der Quelle zu erfassen, zu konsolidieren und zentral bereitzustellen. Die gbo datacomp GmbH aus Augsburg, ein IT-Systemhaus, hat sich auf die Entwicklung solcher MES-Lösungen spezialisiert und bietet Technologien, die selbst komplexe Maschinenparks effizient integrieren.
„Die Ausstattung von Maschinen ist oft sehr unterschiedlich. Deshalb setzen wir auf flexible Schnittstellen wie OPC DA, OPC UA, MT Connect oder Sensoren, um nahezu alle Maschinen zu vertretbaren Kosten in ein MES-System zu integrieren“, erklärt Michael Möller, CEO der gbo datacomp GmbH.
- OPC DA (Data Access): Älterer Standard für Echtzeit-Datenaustausch, geeignet für ältere Maschinen.
- OPC UA (Unified Architecture): Moderner, plattformunabhängiger Standard für sicheren und flexiblen Datenaustausch.
- MT Connect: Ein offener Standard zur Standardisierung von Maschinendaten, der besonders in der Fertigungstechnik verbreitet ist.
Zusätzlich müssen Unternehmen den Schutz sensibler Daten gewährleisten. Zugriffsrechte, Verschlüsselung und sichere Netzwerke bilden die Grundlage für eine sichere Datenverarbeitung. „Ein ganzheitlicher Ansatz ist entscheidend: Datenschutzrichtlinien, regelmäßige Datenüberprüfungen und Mitarbeiterschulungen erhöhen die Sicherheit in einem vernetzten Produktionsumfeld“, betont Michael Möller.
Zweiter Schritt: Daten analysieren
Daten allein bieten keinen Mehrwert – erst durch ihre Analyse entstehen wertvolle Erkenntnisse. Moderne Technologien wie KI und maschinelles Lernen eröffnen hier neue Möglichkeiten, um Produktionsprozesse besser zu verstehen und zu verbessern. Diese Technologien erlauben die Auffälligkeiten in Produktionsdaten zu erkennen und deren Auswirkungen auf die Produktqualität vorherzusagen.
Anwendungen der Datenanalyse:
- Predictive Maintenance: Mithilfe prädiktiver Modelle können Unternehmen den Zustand von Maschinen und Anlagen überwachen und potenzielle Probleme frühzeitig erkennen. Dies minimiert ungeplante Stillstände und optimiert Wartungsintervalle, was die Effizienz erheblich steigert.
- Echtzeitüberwachung: MES-Systeme visualisieren wichtige Kennzahlen wie OEE (Overall Equipment Effectiveness) oder Ausschussquoten, sodass Unternehmen jederzeit die Kontrolle über ihre Produktion behalten.
- Vernetzte Systeme: Standards wie OPC UA ermöglichen die nahtlose Integration von Daten aus verschiedenen Maschinen und Systemen in eine zentrale Datenbasis.
Doch ein Machine-Learning-Modell ist nur so gut wie die Daten, mit denen es trainiert wird. Ungenaue oder unvollständige Daten können zu falschen Ergebnissen führen. Daher sind sorgfältige Datenaufbereitung und Standardisierung unverzichtbar, um zuverlässige Analysen zu gewährleisten.
Dritter Schritt: Prozesse optimieren
Die Erkenntnisse aus der Datenanalyse bilden die Grundlage für gezielte Maßnahmen zur Prozessoptimierung. Besonders innovative Technologien wie digitale Zwillinge spielen hier eine Schlüsselrolle.
Der digitale Zwilling ist ein virtuelles Abbild eines realen Prozesses. Damit lassen sich Szenarien simulieren und Parameter anpassen, ohne die reale Produktion zu stören. Dies ist besonders wertvoll in der Lebensmittelproduktion, wo biologische Prozesse wie Fermentation oft schwer zu kontrollieren sind.
Der digitale Zwilling bietet somit eine Möglichkeit, Produktionsprozesse nicht nur besser zu verstehen, sondern auch gezielt zu optimieren. Die Praxis zeigt, wie Unternehmen durch digitale Technologien und MES-Systeme messbare Erfolge erzielen können. Zwei Fälle aus der Praxis der gbo datacomp GmbH verdeutlichen, welche Potenziale in der Digitalisierung liegen:
- Serienfertiger in der Metallindustrie: Maschinenstillstände wurden durch die Einführung eines MES um 15 % reduziert, wodurch die Produktivität ebenfalls um 15 % stieg.
- Hersteller von Kautschuklösungen: Mithilfe der Digitalisierung der Vulkanisation stieg die Produktivität um 33 %. Die erhöhte Transparenz über Kesselzustände ermöglichte es den Bedienern, schnell zu erkennen, welche Maschine ihre Aufmerksamkeit benötigt. Dadurch konnten die Mitarbeiter mehrere Anlagen gleichzeitig betreuen, ohne die Effizienz zu beeinträchtigen. Die Maschinen wurden optimal ausgelastet, während die Dokumentation von Qualitätsmerkmalen automatisch erfolgte. Abweichungen und Trends wurden online visualisiert, sodass Bediener frühzeitig eingreifen konnten, bevor es zu größeren Problemen kam.
Fazit und Zukunftsaussichten
Die Digitalisierung der Lebensmittelproduktion wird in den kommenden Jahren weiter voranschreiten. KI, Machine Learning und IIoT-Lösungen (Industrial Internet of Things) werden dabei eine zentrale Rolle spielen, da sie die Verarbeitung riesiger Datenmengen und den Schutz sensibler Informationen ermöglichen.
Plattformen wie Manufacturing-X schaffen neue Ansätze für dezentrale Datenökosysteme, während Automatisierung und Robotik die Anforderungen an MES-Systeme weiter erhöhen. Gleichzeitig treiben Nachhaltigkeit, Wissensmanagement und ressourcenschonende Produktionsweisen den Bedarf an präzisen Produktionsdaten voran.
Die Digitalisierung bietet der Lebensmittelproduktion enorme Chancen: von der Effizienzsteigerung über die Reduktion von Kosten bis hin zur Sicherung der Qualität. Unternehmen, die die drei Schritte – Daten erfassen, analysieren, optimieren – konsequent umsetzen, schaffen nicht nur eine zukunftssichere Produktion, sondern gewinnen entscheidende Wettbewerbsvorteile.
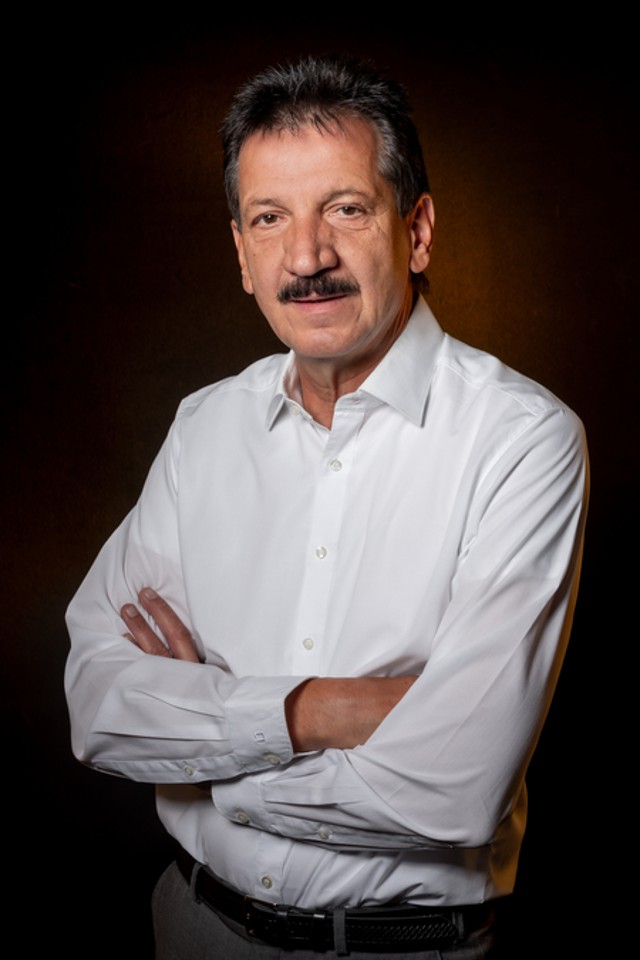
©gbo datacomp GmbH
Für weitere Auskünfte:
Michael Möller
CEO
gbo datacomp GmbH
86150 Augsburg
E-Mail: m.moeller@gbo-datacomp.de
https://www.gbo-datacomp.de/