Maßgeschneiderte Logistiklösungen und Robotik-Systemen.
Herausforderungen in Tiefkühllagern
Tiefkühllager benötigen konstant niedrige Temperaturen (ab -18 °C), um die Warenqualität zu sichern, was zu hohen Betriebskosten führt. Die energieintensive Technik stellt hohe Anforderungen. Um dem Fachkräftemangel entgegenzuwirken, setzen Tiefkühllager verstärkt auf Automatisierung, um manuelle Arbeit bei niedrigen Temperaturen zu reduzieren und die Arbeitsbedingungen zu verbessern. Diese technologischen Anpassungen müssen jedoch im Einklang mit den geltenden rechtlichen Anforderungen und Sicherheitsstandards stehen, die europäische Unternehmen in der Lebensmittelbranche erfüllen müssen:
• Lebensmittelsicherheit und Rückverfolgbarkeit: Eine ununterbrochene Kühlkette gemäß der Verordnung (EG) Nr. 178/2002 ist notwendig. Tiefkühlprodukte müssen bei mindestens -18 °C gelagert und transportiert werden, mit kurzfristigen Abweichungen bis zu 3 °C. Dies gewährleistet Lebensmittelsicherheit und hohe Produktqualität entlang der gesamten Kühlkette.
• Energieeffizienz und Kostenmanagement: Der hohe Energieverbrauch und die steigenden Energiekosten erfordern den Einsatz energieeffizienter Technologien und ein effektives Energiemanagement.
• Sicherheit und Personalmanagement: Angemessene Schutzmaßnahmen, wie kältebeständige Schutzkleidung und regelmäßige Schulungen, sind notwendig, um Unfälle zu verhindern und die Produktivität am Arbeitsplatz zu gewährleisten.
Automatisierungslösungen und Robotik-Systeme
Viele Unternehmen unterstützen die Optimierung von Intralogistikprozessen in Tiefkühllägern durch automatisierte und robotergestützte Technologien.
Die SSI SCHÄFER GMBH & CO KG in Neunkirchen bietet spezialisierte Roboter- und Automatisierungssysteme an. Diese Systeme steigern die Effizienz und senken den Energieverbrauch. Zu den wichtigsten Lösungen gehören:
- - Roboter zur lagenweisen Kommissionierung: Diese Roboter sind bei einem Logistikdienstleister in den USA im Einsatz. Sie optimieren das Handling von Produktlagen und beschleunigen die Kommissionierung.
- - Roboter zur vollautomatischen De-Palettierung und Vereinzelung von Eiscreme durch RO-BER Industrieroboter GmbH, ein Partnerunternehmen der SSI SCHÄFER Gruppe.
- - Roboter zur Kommissionierung von Handelseinheiten (Case Picking): Diese Roboter wurden bei ASKO in Norwegen implementiert und erhöhen die Geschwindigkeit und Genauigkeit der Kommissionierung.
Laut SSI SCHÄFER reduzieren vollautomatische Lagerlösungen den Platzbedarf um bis zu 60 %. Spezielle Regalbediengeräte senken den Energiebedarf um bis zu 25 %. Die Logistiksoftware WAMAS verbessert die Abläufe weiter, zum Beispiel durch die sequenzielle Bereitstellung von Kartons und spezielle Trackingfunktionen, erklärt Dr.-Ing. Dirk Werthmann, Senior Project Engineer Logistics.
Auch die Klinkhammer Intralogistics GmbH aus Nürnberg bietet innovative Lösungen an, die speziell auf die Anforderungen der temperaturgeführten Lagerung abgestimmt sind. Sie nutzt automatisierte Regalbediengeräte und Shuttle-Systeme in Kleinteilelagern, um die Flexibilität und Effizienz zu maximieren. Das Multilevel-Shuttlesystem KlinCAT und ein ebenengebundenes Shuttlesystem wurden erfolgreich in Kühllagern wie bei der Frischdienst Walther GmbH und der Früchte Jork GmbH eingesetzt. Ein weiteres Beispiel ist das 20 Meter hohe Tiefkühllager für den Frischelieferanten Gebrüder Kofler GmbH in Tirol.
Die ProLoCon GmbH aus Niederkassel entwickelt maßgeschneiderte Logistikkonzepte und integriert Roboter in die Planung von Tiefkühllagern. Diese Systeme sorgen für hohe Lagerdichte und effiziente Materialflüsse, auch bei extremen Temperaturen. Durch die Automatisierung werden manuelle Tätigkeiten reduziert, was die Betriebskosten senkt und die Effizienz steigert, betont Christian Manderla, Geschäftsführer der Firma.
Die Integration von Logistikplanung und Automatisierung verbessert die Abläufe in der Lagerlogistik. Dadurch werden Effizienz und Flexibilität gesteigert. Experten betonen die Bedeutung von Echtzeit-Daten und technologie- sowie herstellerneutralen Planungsansätzen. Diese Ansätze verbessern die Entscheidungsfindung und erhöhen die Anpassungsfähigkeit. So wird der Lagerraum optimal genutzt und die Kosten entlang der Lieferkette gesenkt. Unternehmen können dadurch schneller und besser auf Marktveränderungen reagieren.
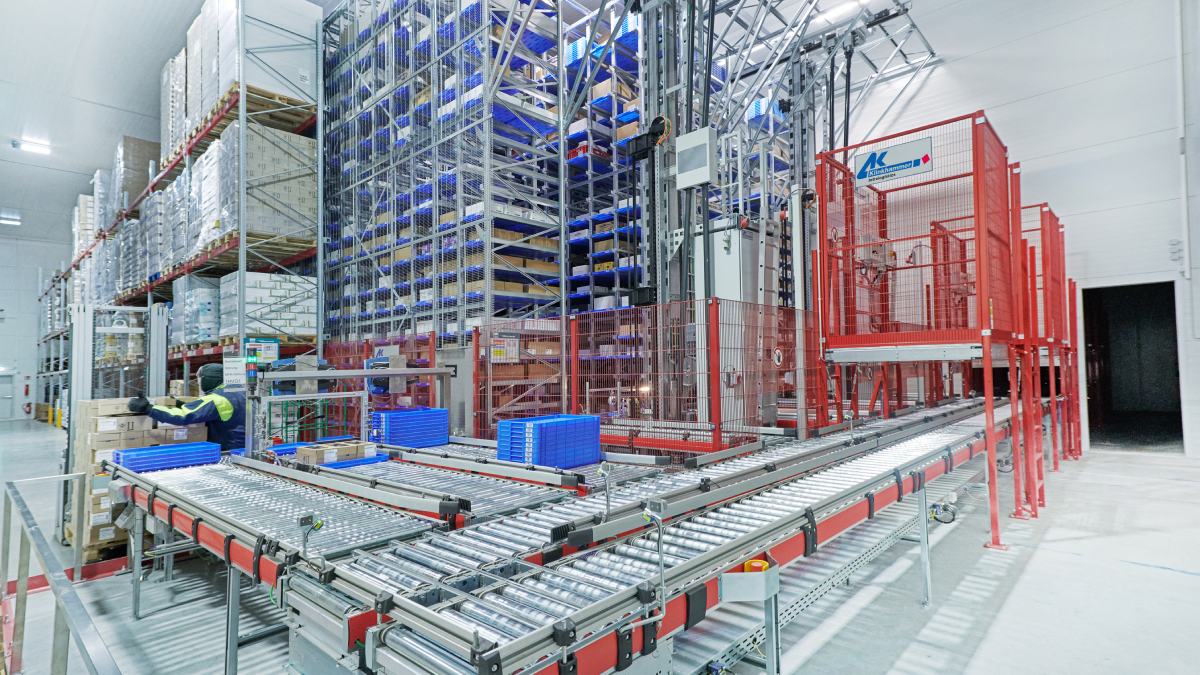
©Klinkhammer Intralogistik GmbH
Herausforderungen, Zukunftsaussichten und Nachhaltigkeit
Die Kühllagerlogistik steht vor Herausforderungen durch hohen Energieverbrauch und strenge Nachhaltigkeitsanforderungen. Moderne Automatiksysteme, wie die von Klinkhammer, nutzen Energierückgewinnung und Power Caps, um den Energieverbrauch zu senken und die Effizienz zu steigern – ein entscheidender Vorteil angesichts steigender Energiekosten und Fachkräftemangel. Bei einem Lagersystem mit Power Caps wird die Bremsenergie des Regalbediengeräts direkt im Antriebssystem für die nächste Beschleunigungsphase zwischengespeichert. Technologien wie patentierte Gegengewichte und Netzrückspeisung reduzieren die Abwärme und erfüllen die Anforderungen an Energieeffizienz und Nachhaltigkeit, erklärt SSI SCHÄFER.
Zukünftig wird eine stärkere Automatisierung in Tiefkühlumgebungen angestrebt, um Unternehmen bei der Effizienzsteigerung und Kostensenkung zu unterstützen. Zahlreiche Aussteller präsentieren auf der Messe nachhaltige Logistikkonzepte, die erneuerbare Energie und effiziente Technologien nutzen, um den Energieverbrauch zu reduzieren.
Fazit
Der Fachkräftemangel, steigende Energiekosten und die wachsende Nachfrage nach Tiefkühlprodukten erhöhen den Bedarf an effizienteren und nachhaltigeren Lösungen in der Tiefkühllagerlogistik. Der Einsatz von Robotersystemen kann je nach Anwendungsfall erhebliche Vorteile bei der Einsparung von Energie- und Personalkosten bieten. Die Anfangsinvestitionen sind hoch. Experten erwarten jedoch, dass diese Technologien langfristig Einsparungen bringen und die Effizienz steigern.