Weniger Energie und Platz durch Vakuum
Die Schubert Gruppe blickt zum Beispiel auf eine jahrzehntelange Erfahrung bei der Verpackung von Lebensmitteln zurück. Das Crailsheimer Familienunternehmen setzt bei seinen digitalen, roboterbasierten Verpackungsmaschinen auf ein Zusammenspiel von einfacher Mechanik, intelligenter Steuerungstechnik und Modularität. Den Nachhaltigkeitsaspekt geht das Unternehmen mit dem Geschäftsbereich Schubert Consulting und dem neu gegründeten Packaging Competence Center (PCC) interdisziplinär an. Dabei behandeln jeweils Experten Material und Technologie, inklusive deren Automatisierung, im Kontext von Gesetzesvorgaben und Markt.
Materialeinsatz
Das Schubert Packaging Competence Center sieht wichtige Stellschrauben für eine nachhaltige Verpackung von Backwaren vor allem beim Material, wobei Karton oder Monofolien mit Blick auf die Nachhaltigkeit bevorzugt werden sollten. Zugleich geht es darum, beim automatisierten Zuschnitt durch Robotertechnologie die Vorlagen möglichst optimal auszunutzen. Materialdicke und Eigenschaften sollten dabei möglichst so sein, dass sie auf den vorhandenen Maschinen verarbeitet werden können.
Oft lassen sich durch eine entsprechende Überarbeitung der Formate mit kleineren und einfacheren Schnitten oder dünneren Trays auf Dauer deutliche Mengen Material einsparen, heißt es ergänzend. Die gleiche Zielrichtung steht hinter einer aktuellen Idee der Schubert-Experten für optimierte Multipacks mit Muffins oder ähnlichen Gebäcken. Normalerweise erfolgen Zuschnitt und Faltung solcher Trays nach einer Vorlage, die den Boden und das Oberteil mit Lochmarkierungen für die Gebäcke umfasst. Bei dem dreidimensional gedachten Vorschlag, den die Kartonagehersteller vermittelt bekommen, werden die Ausschnitte für die Öffnungen dagegen nach unten gebogen und dienen auf diese Weise direkt als Bodenstütze für die Produktförmchen oder Becher; die Materialfläche für einen extra Boden entfällt. Neben einer Materialeinsparung von rund 40 Prozent und weniger Abfall bei den Kartonherstellern, profitierten diese gewichtsbedingt von einem geringeren CO2-Fußabdruck beim Transport zum Kunden, stellt Michael Graf, Director PCC fest
Alternative zu geleimten Kartons
Im Zusammenhang mit nachhaltigen Verpackungsmethoden verweist er außerdem auf die neue Dotlock-Technologie für eine leimfreie Kartonherstellung: Statt die Ecken mit erhitztem Leim zu verkleben oder mit einem höheren Materialverbrauch zu falten, liegt der Clou allein in einer mechanischen Technik: Ähnlich wie bei dem sogenannten Clinchen zum Fügen von Metallplatten werden die Kartons von einer Seite mit mehreren nadelartigen Stiften durchstochen und die nach hinten herausragende Lochkragen durch Pressdruck zu einem stabilen Formschluss gebogen. Die Dotlock-Kartonlösung sei vollständig über den Papierkreislauf recycelbar, sagt Graf. Möglich seien aber auch Karton-Monofolie-Hybridlösungen, die ebenfalls in den Recyclingkreislauf könnten.
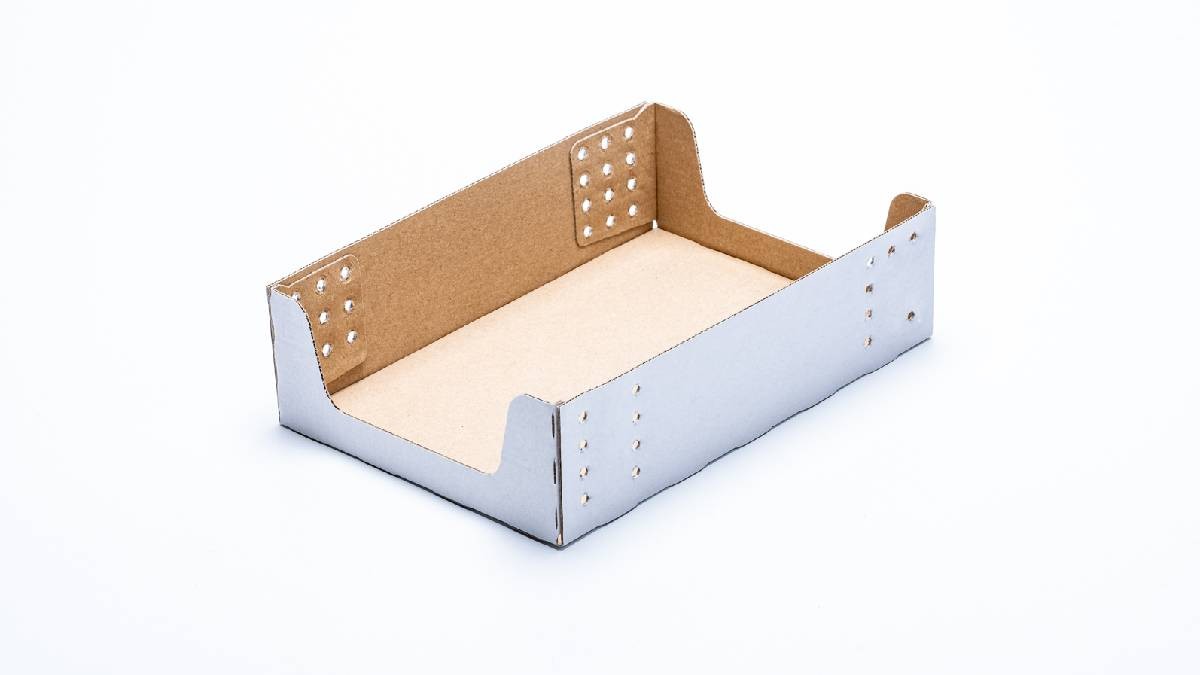
Neue Dotlock-Technologie für eine leimfreie Kartonherstellung. © Gerhard Schubert GmbH
Mit weniger Energieverbrauch nachhaltiger werden
MULTIVAC aus dem süddeutschen Allgäu, ebenfalls Experte für industrielle Verpackungs- und andere Maschinen, hat dagegen aktuell unter anderem den Aspekt der Energieeinsparung beim Verpacken von frisch gebackenen Backwaren in den Blick genommen. Nachdem sie aus dem Ofen kommen, werden Brote-, Fein- oder Kleingebäcke normalerweise zunächst über Kühlspiralen bei Umgebungstemperatur oder in langen Kältetunneln abgekühlt und anschließend folienverpackt. Beim innovativen neuen Cooling@Packaging-System von MULTIVAC laufen beide Schritte stattdessen hygienisch und kombiniert in einer einzigen Maschine ab.
Bei dem Verfahren positionieren Einlegeroboter die etwa 95 °C heißen Produkte direkt vom Ofen kommend in vorgeformte Tiefziehpackungen. Anschließend wird in den Kammern ein Vakuum angelegt, wodurch in den Lebensmitteln enthaltene Feuchtigkeit entweicht und die gleichzeitig freiwerdende Verdunstungsenergie diese innerhalb von wenigen Sekunden auf 30 °C herunterkühlt. Die Packungen würden in mehreren Kammern zwischen Form- und Siegelstation hintereinander vakuumiert, wobei die Anzahl der Cooling@Packing-Stationen produkt- und leistungsabhängig sei, erläutert Produktmanager Thomas Fickler den Prozess genauer. In der letzten Kammer vor der Heiß-Siegelstation betrage das Endvakuum dann circa 20 mbar.
Nach Unternehmensangaben ist das Verfahren für das Hochleistungssegment geeignet, wobei Anwender nach derzeitigem Stand ihre marktüblichen Verpackungsmaterialien wie PA/PE-Folien weiter nutzen können. Im vergangenen Herbst mit dem Deutschen Verpackungspreis des Deutschen Verpackungsinstituts e.V., dvi auszeichnet, steht Cooling&Packaging kurz vor der Markteinführung. Wie Fickler auf Nachfrage sagt, lasse sich der Ansatz prinzipiell auch auf andere Lebensmittel übertragen. Dies müsse aber mit Tests spezifisch verifiziert werden.